Alumina Tiles And Composite Liners
Our ceramic range has three different alumina composition (92%, 95% and ZTA) products to suit the various mining applications.
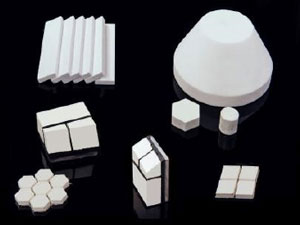
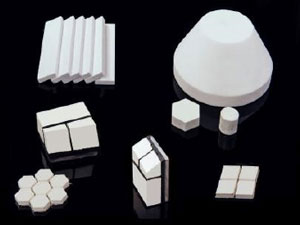
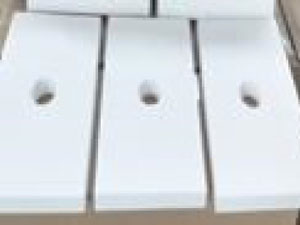
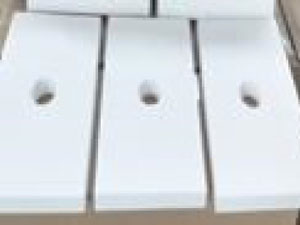
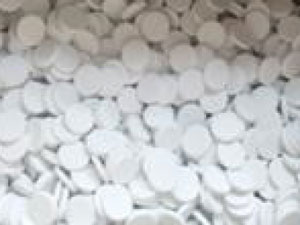
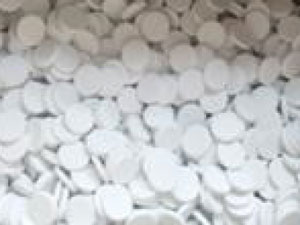
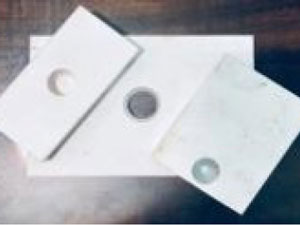
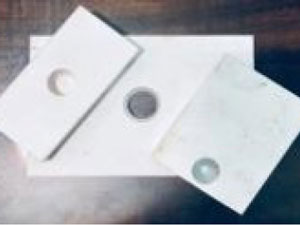
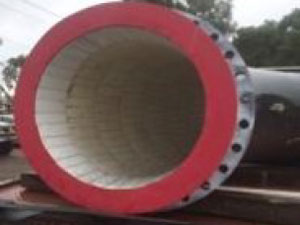
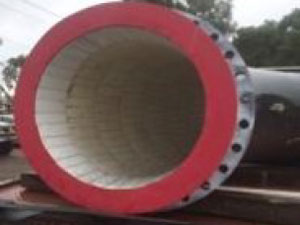
Composite Ceramic Liners & Mats
REXLINE™ ceramic wear liners range include composite ceramic liners or Steel backed and studded as per requirements. We also have a range of molded ceramic in rubber with CN backing. The liners can be customized depending on the application.
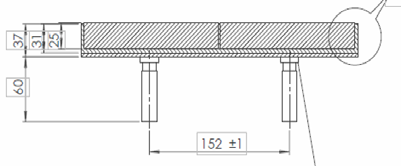
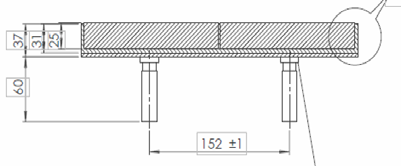
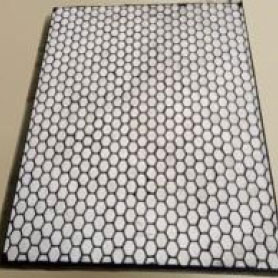
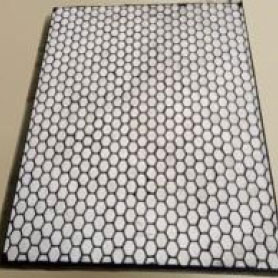
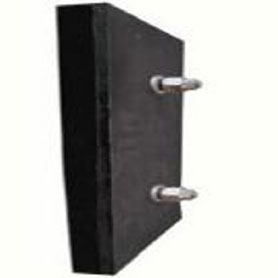
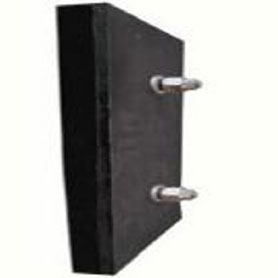
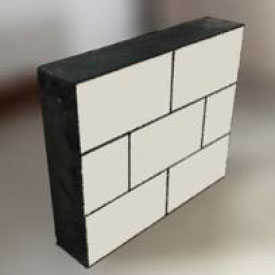
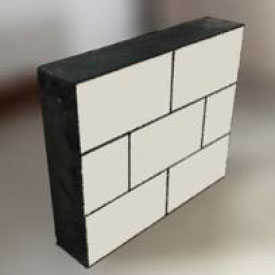
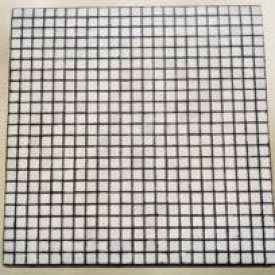
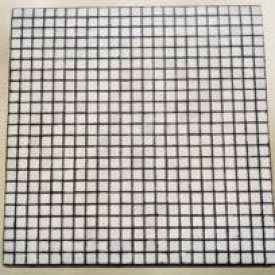
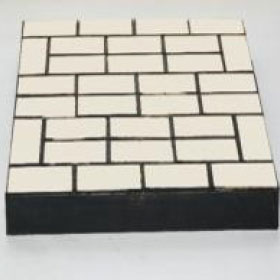
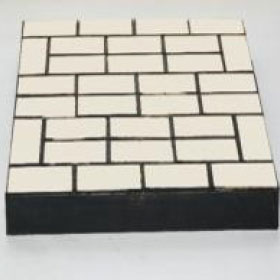
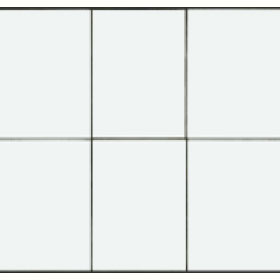
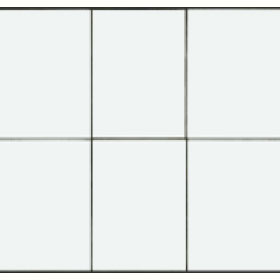
Ceramic Liners Tile Format
Steel Backed Ceramic Liners | ||||
Tile Thickness | Tile size in mm | Rubber in mm | Steel in mm | Liner Sizes (mm) |
32mm | 20 | 6 | 6 | 300/150, 300/300, 300/450, 300/600, 450/450 |
64mm | 50 | 8 | 6 | 300/150, 300/300, 300/450, 300/600, 450/450 |
37mm | 25 | 6 | 6 | 300/150, 300/300, 300/450, 300/600, 450/450 |
69mm | 55 | 8 | 6 | 300/150, 300/300, 300/450,,300/600, 450/450 |
Ceramic Liners Tile Format
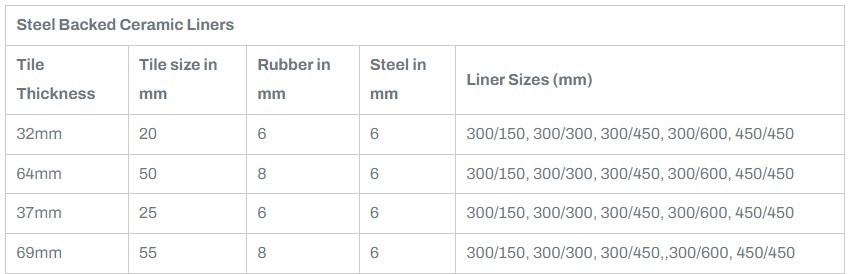
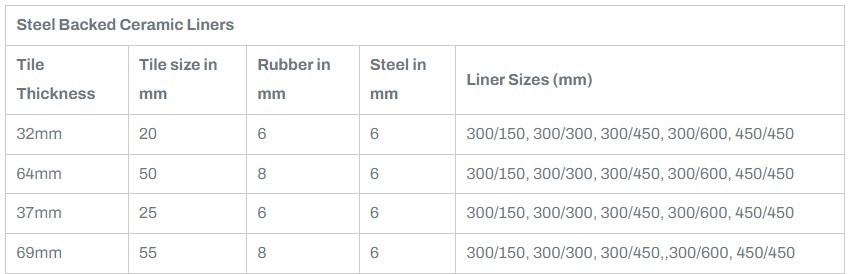
Composite Ceramic Data Sheet
Technical Data of the Ceramics | |||
Description | 92% Ceramics | 95% Ceramics | ZTA |
Alumina Content | 92% | 95% | – |
Density (g/cm³) | 3.61 | 3.62 | 4.1 |
Rockwell Hardness (HRA) | 85 | 88 | 90 |
Vickers’ Hardness (HV10) | 1200 | 1350 | 1400 |
Fracture Toughness (KIC or MPa.√m) | 3.6 | 4.1 | 5.5 |
Compressive Strength (MPa) | 2000 | 2281 | 2924 |
Wear Volume (cm³) | 0.02 | 0.017 | 0.009 |
Composite Ceramic Data Sheet
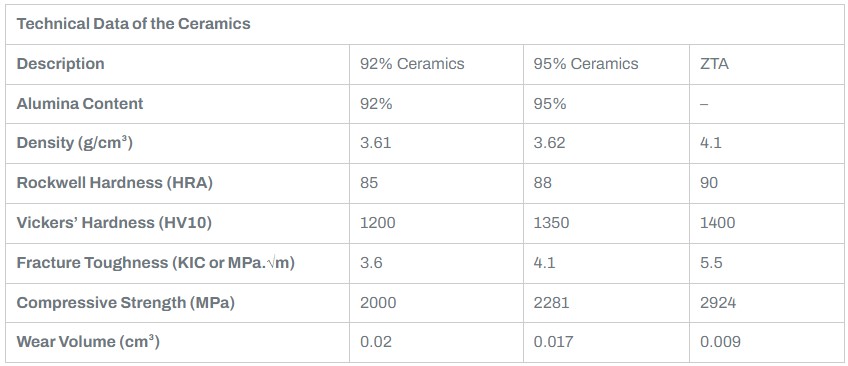
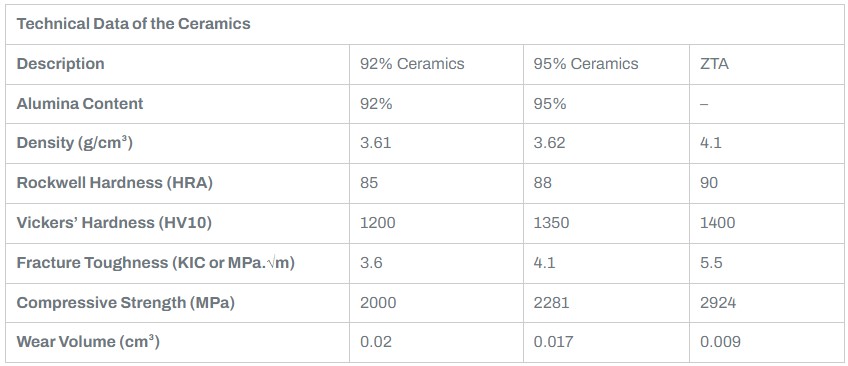
Technical Data of the Rubber | |
Items | Index |
Elongation | ≥ 450% |
Tensile Strength | ≥ 180 MPa |
Break Extension | ≥ 500% |
Shore Hardness | 55 – 65 HA |
Tear Strength | ≥ 70 KN/M |
Break Permanent Deformation | ≤ 24% |
Rubber and Ceramic Adhesion Force | ≥ 3.0 MPa |
(Shearing Stress) | |
Temperature Resistance | ≤ 100˚ C |
Rubber Aging Life | ≥ 8 years |
Gap Between Tile | 0.8 – 2.0 mm |
Rubber Edge | 1.5 – 2.0 mm |
PanzerPoxy High Density Ceramic Epoxy Repair Kit
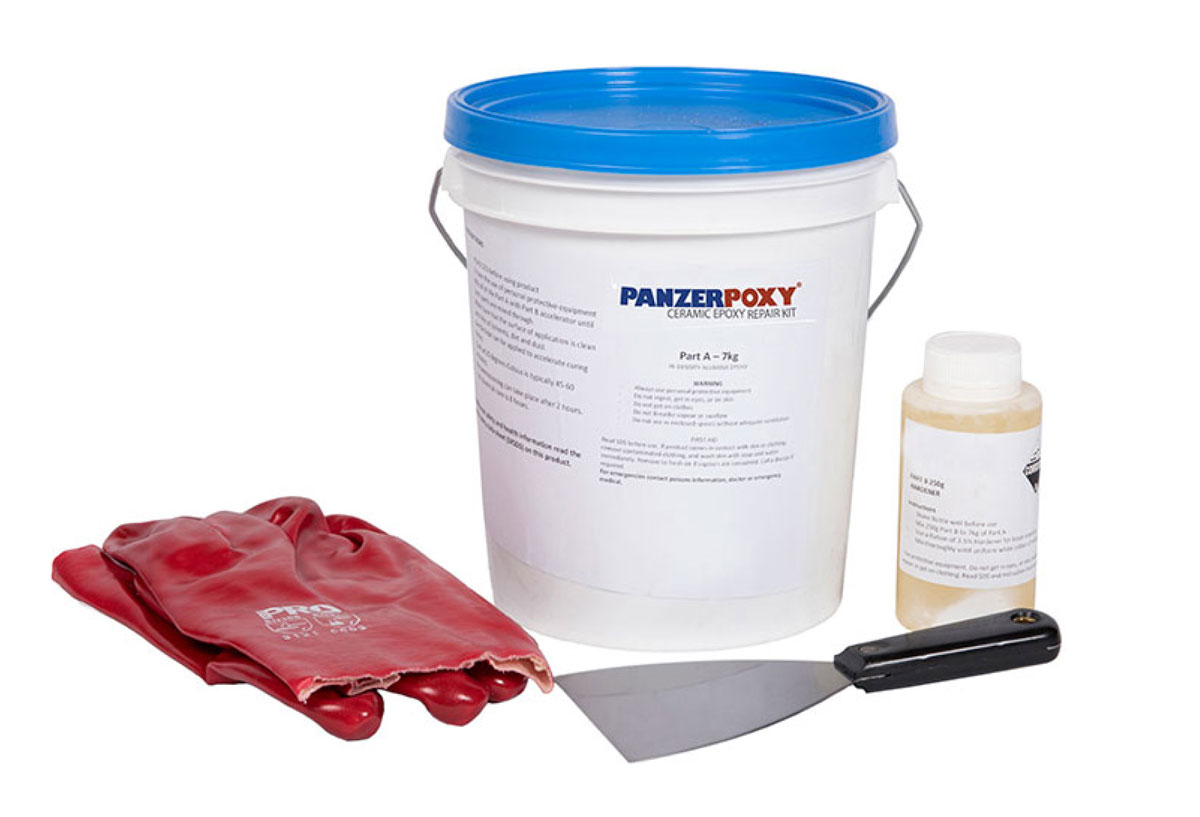
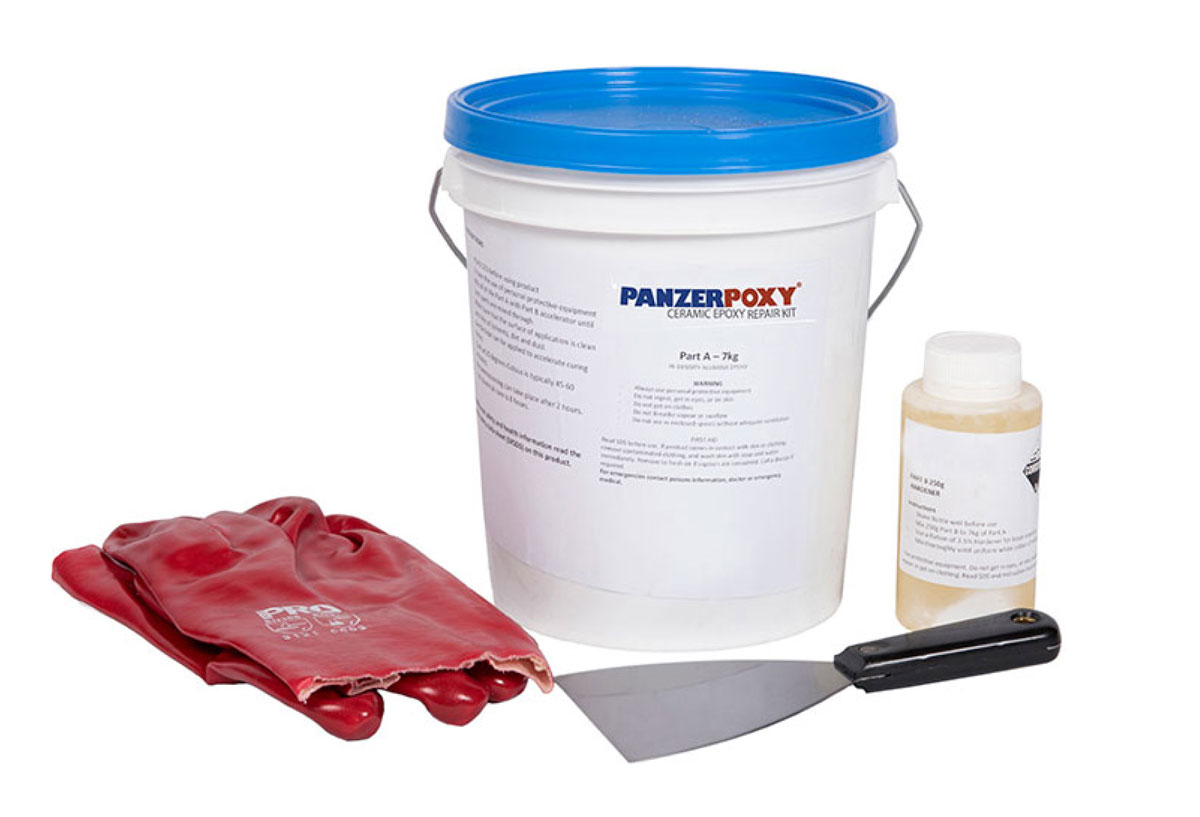
PANZERPOXY Hi-Density Fast Cure Alumina Wear Epoxy is a 2-part epoxy ceramic wear resistant material, extensively used for repairing and protecting surfaces against abrasive attack.
PANZERPOXY contains 15% pure solid white beads, at an alumina content of 92-95 %.
The remaining alumina as is equivalent to that, which is in all ceramic wear epoxy on the market with most material being currently only at a total of 78% – 81% alumina content.
PANZERPOXY is a two part epoxy ceramic wear resistant material that provides the following product characteristics:
- Excellent sag resistance
- High trowel ability
- No shrinkage
- High slump resistance
- High peel strength from substrate
- Low fumes – Low VOC
- High impact and abrasion resistance
- Can be used on wet and damp surfaces
PANZERPOXY is designed to minimize sliding abrasion and corrosion wear. When used by itself, equipment, life can be extended by direct application to ceramic, concrete, steel, and rubber substrates where it exhibits very high peel strength. It also can be reapplied to itself and other ceramic coatings or used as a top coat to prolong wear life. Typical uses include: cyclone linings, pump linings, chutes, hoppers, pipes, pipe bends, tile grouting, dust collectors and exhausters, etc
TECHNOLOGY | EPOXY |
Chemical type (resin) | Bisphenol A resin |
Chemical type (hardener) | DETA |
Appearance (resin) | Clear/White |
Appearance (hardener) | Amber |
Appearance (mixed) | Clear |
Components | Part A & Part B |
Mix ratio by volume | 4:1 – Part A : Part B |
Cure | Room Temp @ 25˚C |
Tack time/Gel time | 40 min @ 25˚C |
Total cure time | 8 hours @ 25˚C |
Ceramic | AI2O3 |
Ceramic type | Fused AI2O3 |
Ceramic grit size | >80% 0.5 to 1.0 mm |
Colour mixture | Bronze/Black/White |
Epoxy/Ceramic ratio | >68% w/w ceramic |
CHARACTERISTICS | TYPICAL VALUE |
Appearance | Bronze/black pas |
Coverage | 2.8 kg-1 sqm at 1mm |
Working life | 40 mins @ 25° C |
Compressive Strength | 9,000 (N/mm2) |
Hardness ASTM D 2240 | 88 Shore D |
Peak exotherm | 55°C |
Tensile strength | 9,500 psi |
Flexural strength | 16,000 psi |
Izod impact, ft lbs/in | 0.54 |
Weight loss @ 100°C | 0.4% |
Volume resistivity | 1.4 × 1015 (ohm cm) |
Dielectric const @ 10 6 Hz | 4.26 |
Typical Properties of Cured Material
To achieve product best use and performance, thorough mixing is required.
Application with a clean dry trowel achieves best results. A smooth finish can be obtained without the use of water or oil, typically 20 mins after mixing when best workability is possible. Heating can be applied to accelerate cure time. Thick applications cure faster due to the exothermic reaction of the reactants.
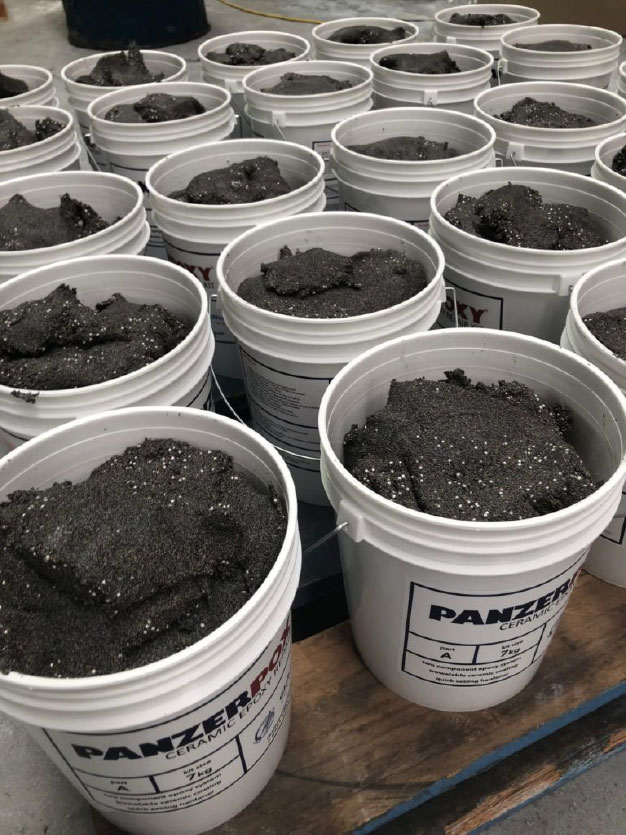
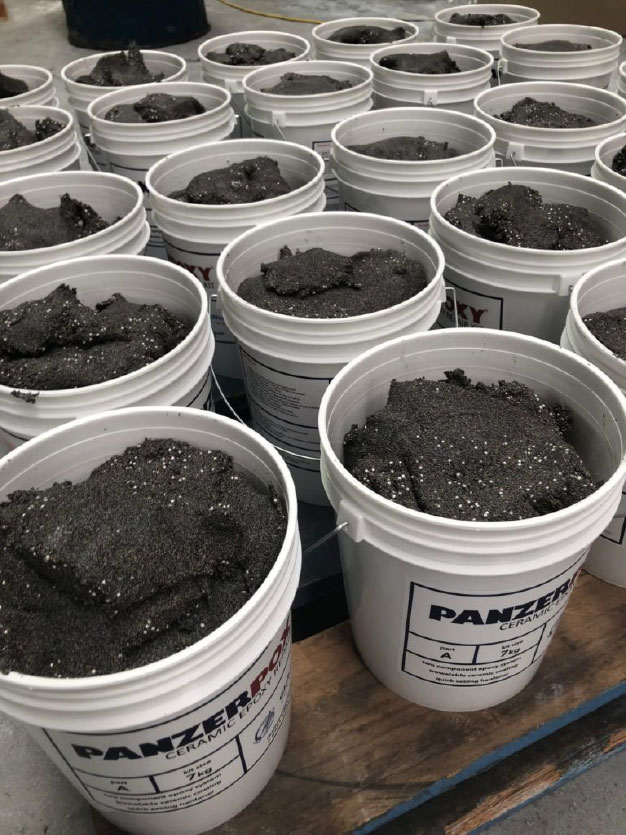
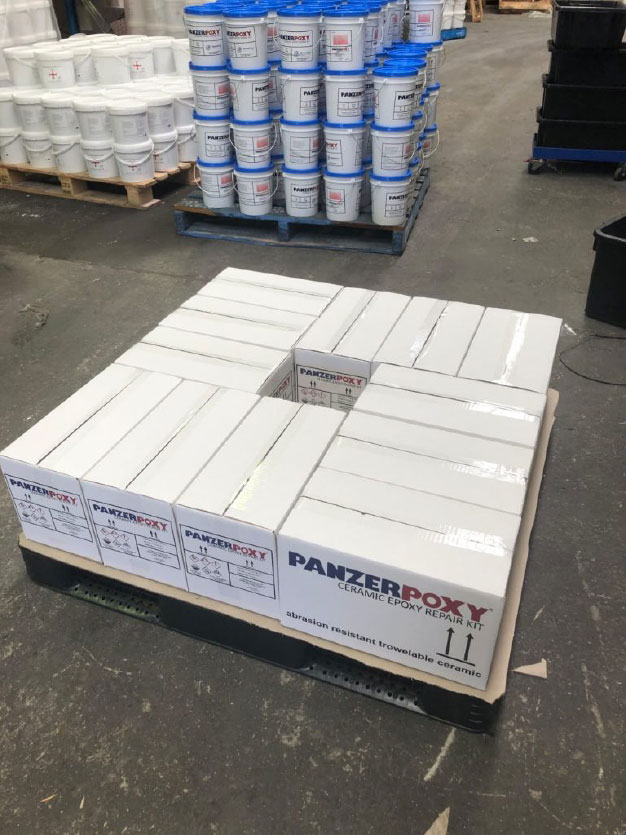
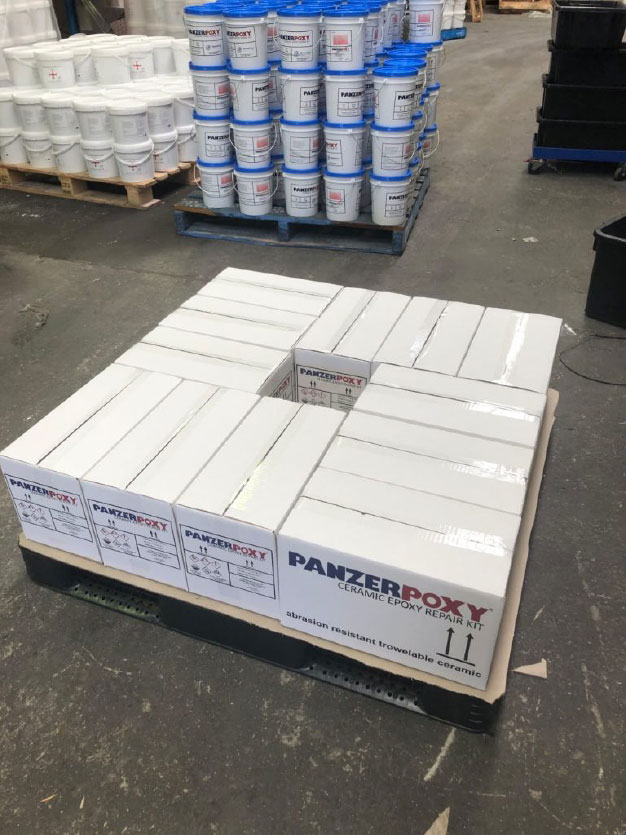