TRUCK BED LINER
PROJECT DETAILS
Project Name | Dump Truck Lining |
Document ID | #0785 |
Problems & Challenges
Rexline Engineering can take up the challenge to design an effective liner package for truck body to overcome the localised wear issues and meet the miner’s productivity, performance and reliability requirements.
A truck and shovel operation, the mine operates Komatsu model’s 785 off-road haul trucks, fitted with Komatsu OEM bodies. Commissioned in Polavaram, India both truck fleets were operating well within Komatsu’s operational parameters however the aging bodies on the fleet of 400 trucks were no longer economic to maintain. The site maintenance team were concerned about the productivity losses stemming from the trucks’ unscheduled maintenance and repair requirements.
Hauling trucks/Excavator Buckets have the standard designed body with the wear package which are normally heavier than the recommended gross mass of body.
The challenge for Rexline Engineering Reliability and Engineering team was to design and manufacture a truck body that would be compatible with the Komatsu 785 truck, overcome the localised wear issues and meet the miner’s productivity, performance and reliability requirements.
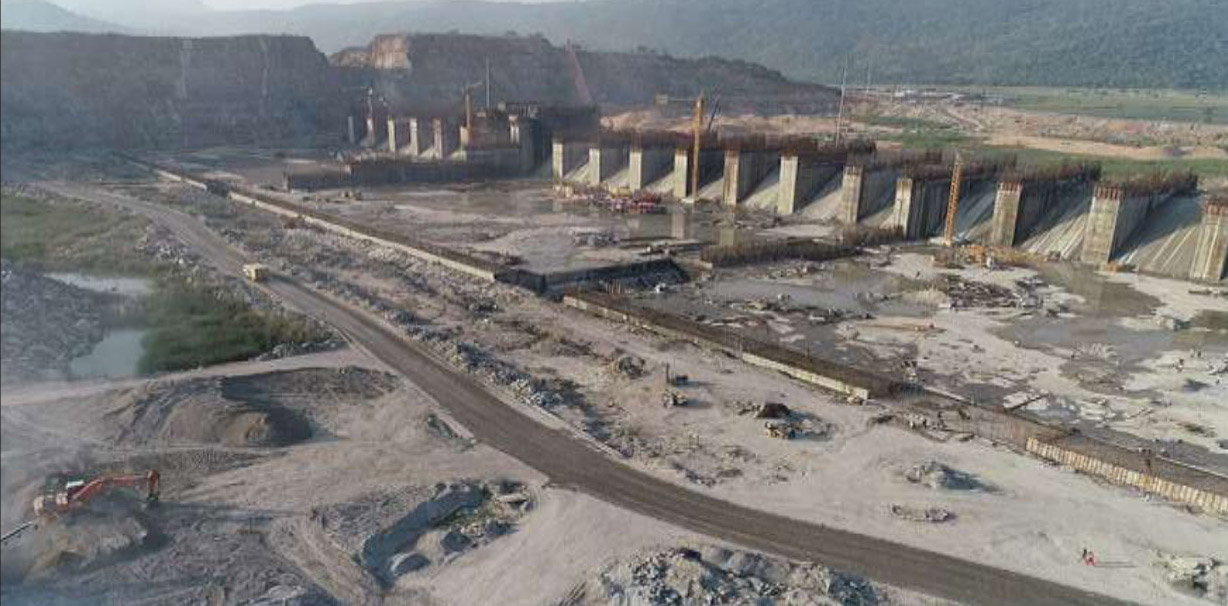
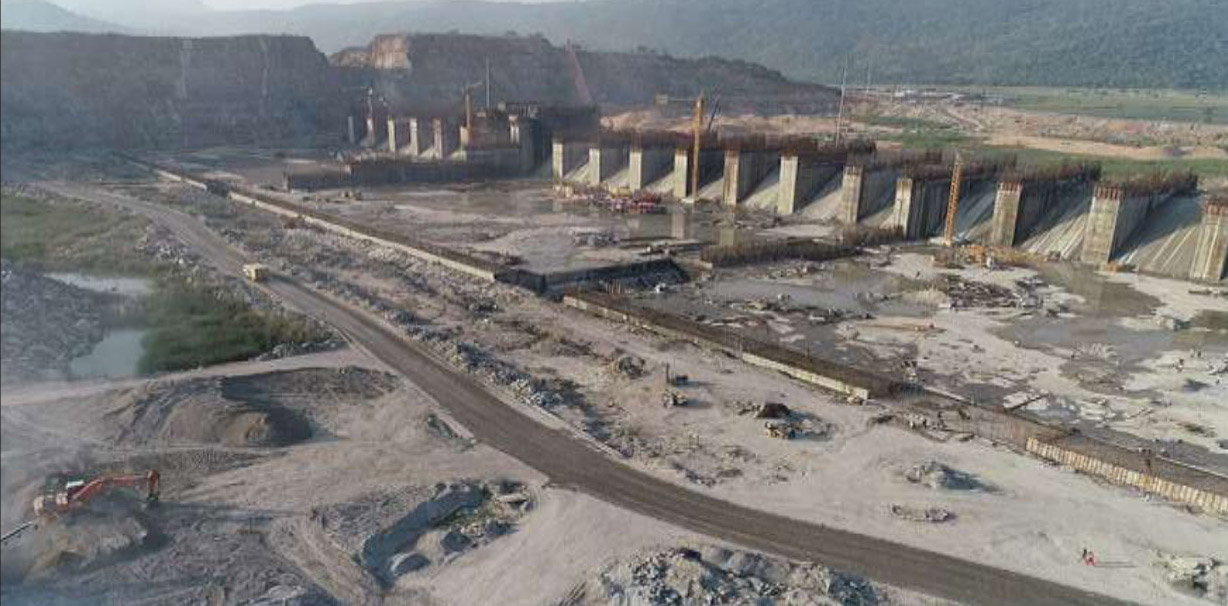
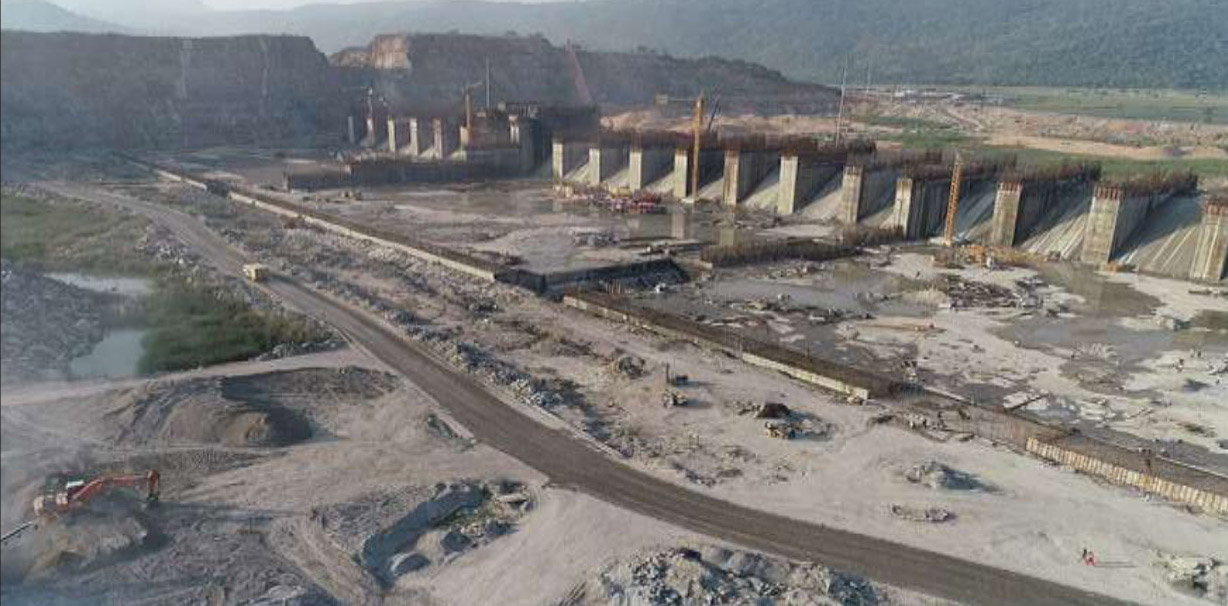
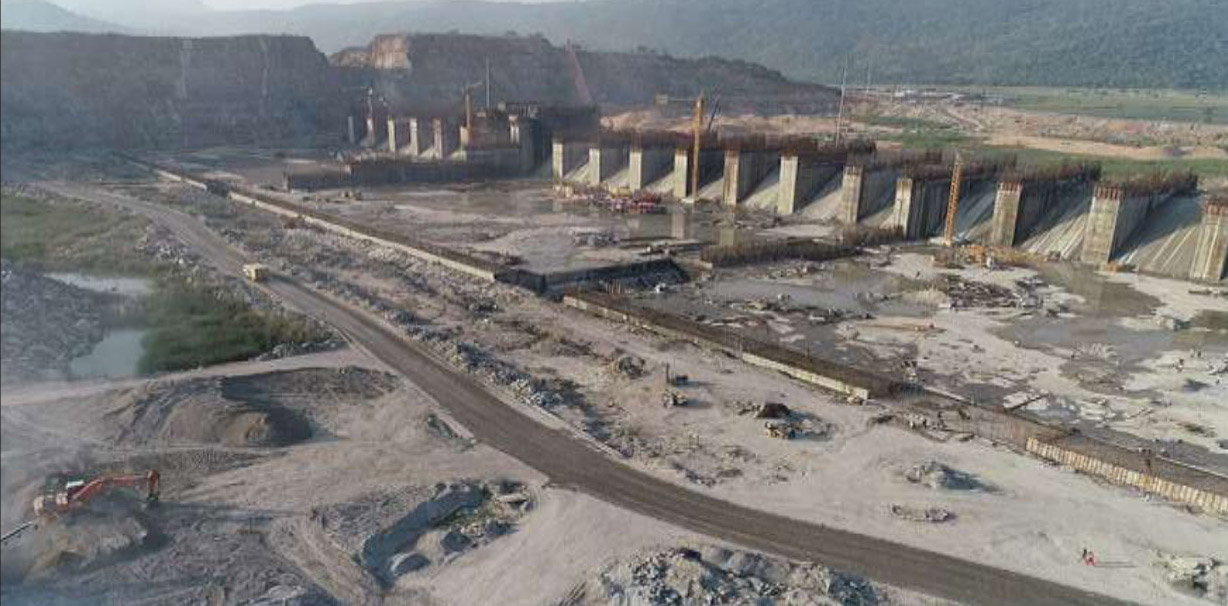
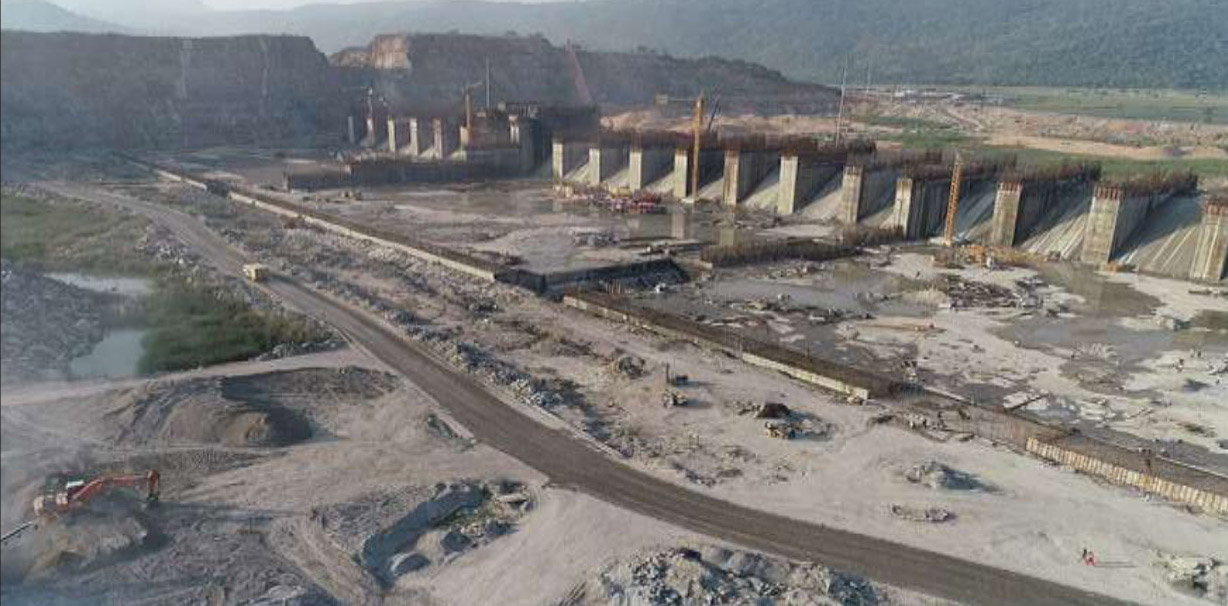
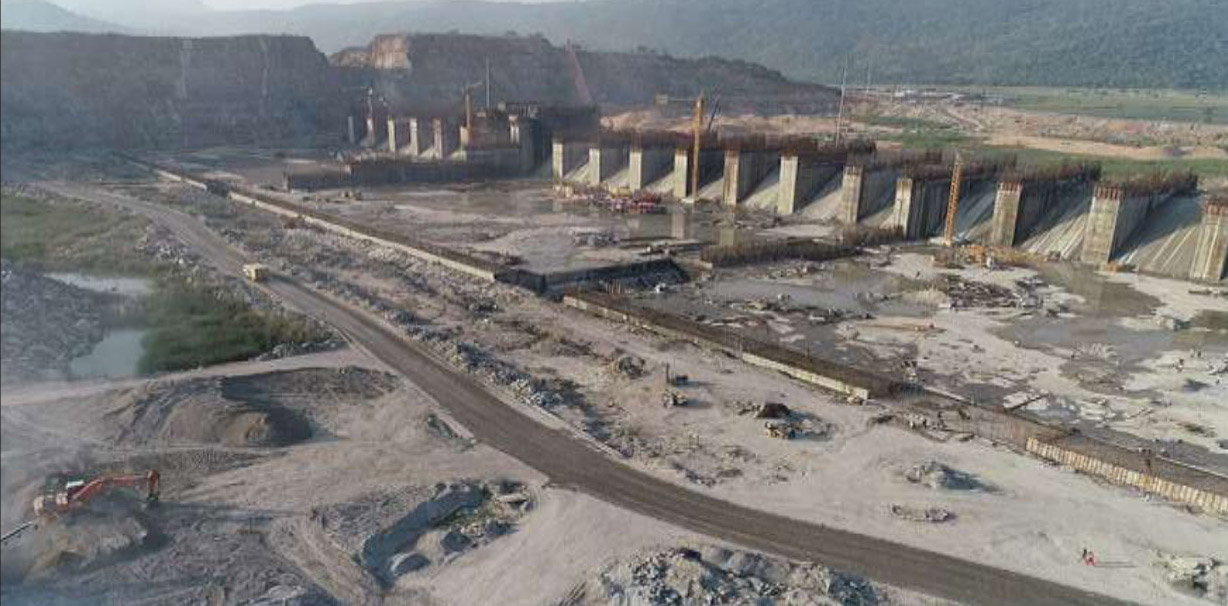
The data required to recommend the suitable product for the application
- Photos of the current high wear areas
- Current liners used – Brand
- Current liners chemical compositions
- Current liners physical properties
- The bucket and Truck tray drawings
- Thickness of the liners
- Service life data and any history
- Type of ore
- Total weight added to the trays and the buckets
- Current methodology of fastening
Our Solutions
The client provided with comprehensive Rexline Engineering documentation which included details of the unique site-based requirements and key performance indicators (KPIs) the miner had for the replacement bodies.
Armed with this information, along with OEM dimensions around total truck weights, operating weights, optimum load characteristics and feedback from site personnel, Rexline Engineering designed and fabricated an SAWT ULTRACLAD liner kit, fully customised to maximise payload capacity, to fit the KOMATSU 785 chassis.
Our engineering and project management team in conjunction with our client will execute a full potential project to identify weight reduction strategies, wear life extension and reduce downtimes.
As part of the design, the wear material was substituted for a more fit-for-purpose product and the effective liner arrangement was proposed which further would enhances the cost savings. The team identified the opportunities and was engineered, proven and passed through a change management process and once all stakeholders agreed and approved, the initiatives were then implemented.
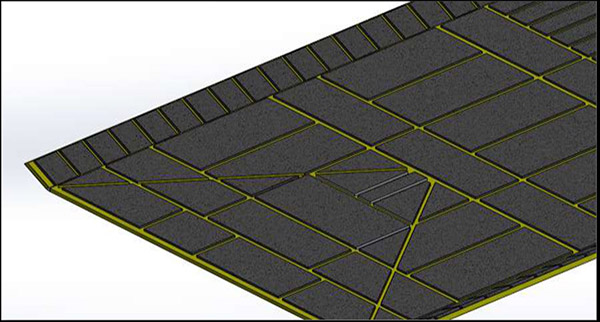
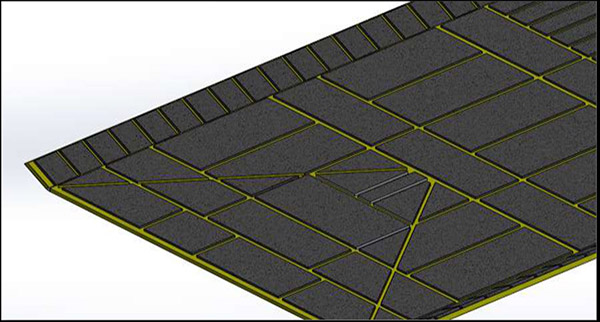
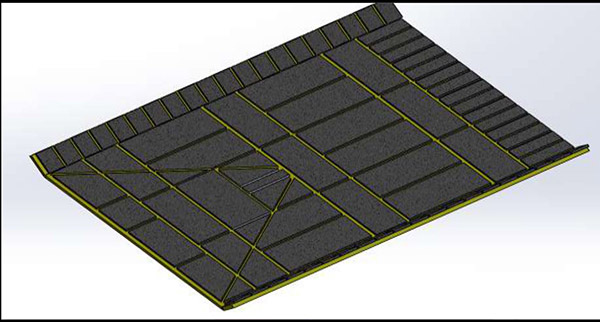
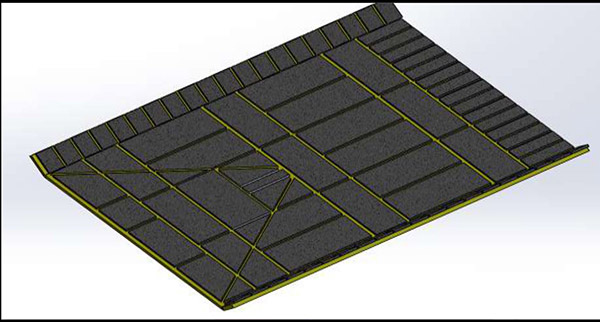
Inspection after 14 months of Installation
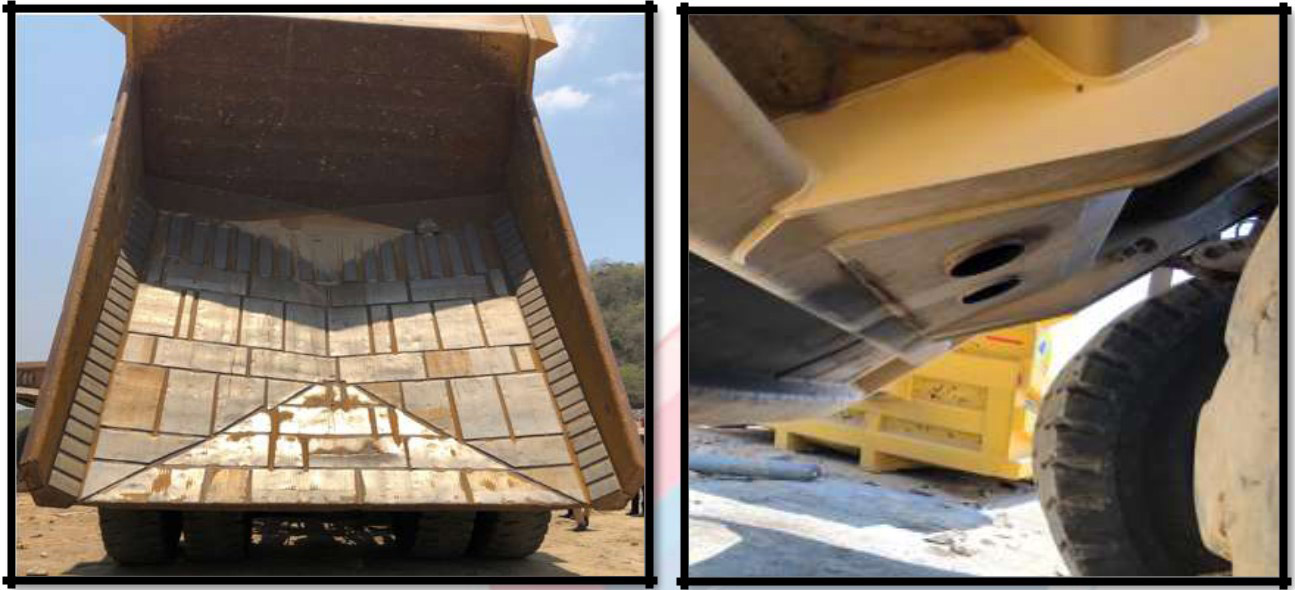
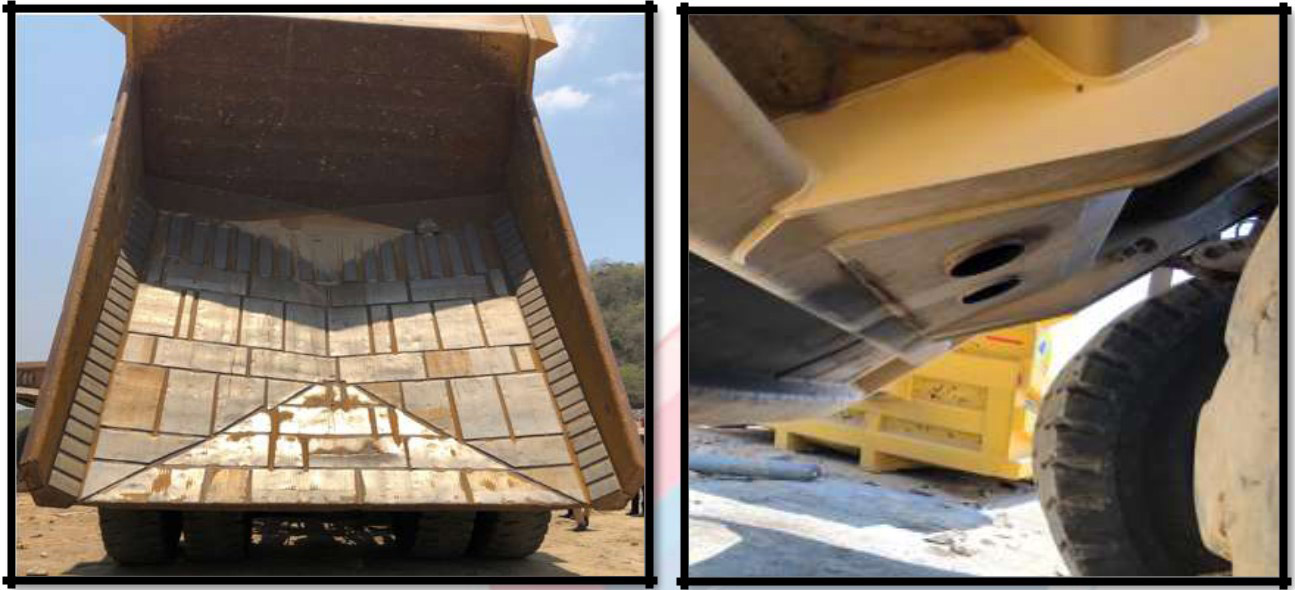
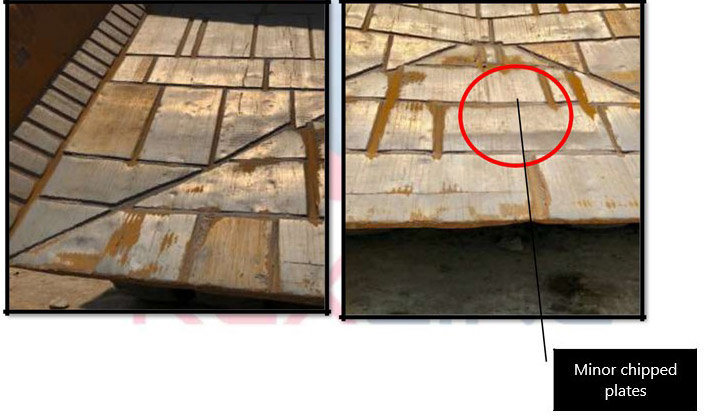
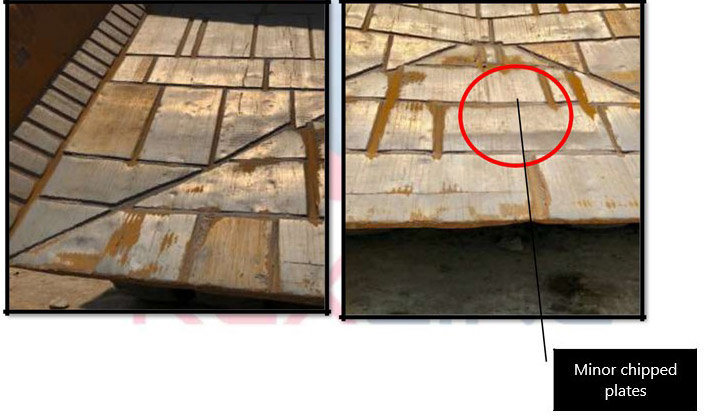
Liners are still in good condition; the wear is very minimal and no major cracks on plate. Several chipped plates were observed. This is due to the transfer of heat from underneath the truck body where the main exhaust is situated.
The Results
Achieving and exceeding KPI bcm target. The average payload for the truck body is 92t, which is over the original target of 90t. Increase in capacity translates to extra 2 1⁄2 truckloads per hour across the fleet.
The Rexline Engineering liners kit body is currently not volumetrically limited when it comes to hauling waste material.
No structural cracking and virtually no wear to date.
Floor replacement expectation is now 18 months– extended from the original 12 months.
- Reduction in fuel burn on empty haul
- Reduction in tyre wear on empty haul
- Improved cycle times due to improved wear products
- Reduced risk of loose metal events due to improved wear package layout
- Reduction in overload occurrences
- Improved volumetric capacity with increased payload potential
- Reduction in operational costs due to wear package technology
- Reduction in damage occurrences through design change
- Elimination of hidden carry back
- Individual models comply with OEM specifications
- Less maintenance
- Increase Production
- Regular Wear Audits & Assessments
- Option of slot welding or direct welding plates
- High percentage of chromium which can withstand extremely high wear and impact.
- Lighter weight
- Regular Report Generated to Take Remedial Measure
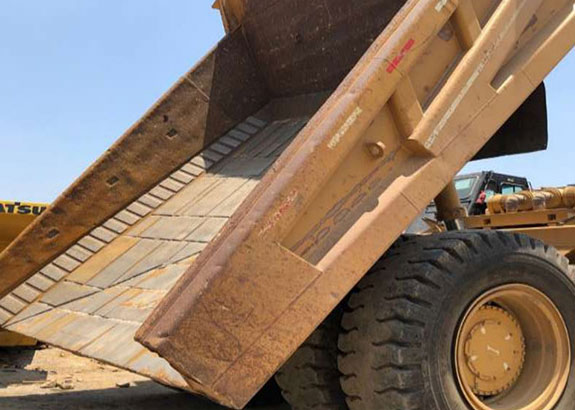
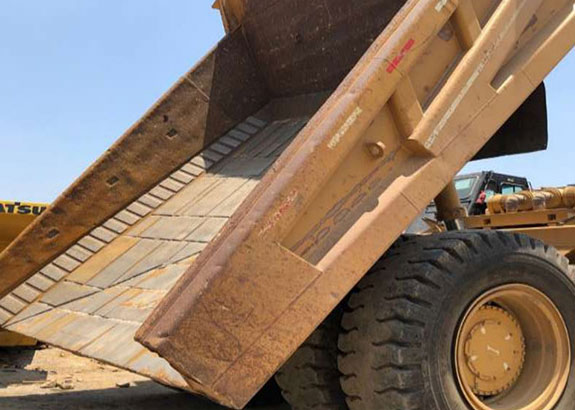